Applications
Our competitive edge lies with the knowledge and experience of our validation personnel. This provides us with insight in the current validation needs and an intimate understanding of cGMP’s along with a keen awareness of equipment design and practical production requirements.
From design qualification (DQ) through installation qualification (IQ), operational qualification (OQ) and process qualification (PQ) we are able to develop a tablet press and press control validation package to suit you.
From design qualification (DQ) through installation qualification (IQ), operational qualification (OQ) and process qualification (PQ) we will use an efficient, systematic, risk based, quality system approach to developing a validation package to suit your mixing and granulating equipment.
Validating a fluid bed coater? From design qualification (DQ) through installation qualification (IQ), operational qualification (OQ) and process qualification (PQ) we can develop a package to suit you.
Are you using a side vented tablet coater? From Accelacota to Hi-coater, SMB will develop a validation package to satisfy your design qualification (DQ), installation qualification (IQ), operational qualification (OQ) and process qualification (PQ) requirement.
Vial filling, plugging. Capping and Over-crimp. From design qualification (DQ) through installation qualification (IQ), operational qualification (OQ) and process qualification (PQ) we are able to develop a package to suit your need.
Vision and Laser absorption spectroscopy inspection systems. From design qualification (DQ) through installation qualification (IQ), operational qualification (OQ) and process qualification (PQ) we can develop a package to suit you validation requirement..
Vision Systems are increasingly utilized for Product Analysis, Package Inspection, Code Inspection, Verification, Recognition and Comparison. SMB has decades of experience in Vision System Engineering, Development and Validation. From design qualification (DQ) through installation qualification (IQ), operational qualification (OQ) and process qualification (PQ) we are able to develop a Vision Inspection validation package to suit you.
Experience counts. You can count on SMB to fulfill your validation need. From design qualification (DQ) through installation qualification (IQ), operational qualification (OQ). process qualification (PQ) and standard operating procedures (SOP) we are able to develop a package to suit you.
From piston filler through rotary volumetric, peristaltic, level and net weight fillers. From design qualification (DQ) through installation qualification (IQ), operational qualification (OQ) and process qualification (PQ) we will use an efficient, systematic, risk based, quality system approach to developing a validation package to suit your requirements.
Be it high speed or low, Inline or rotary, pressure sensitive, glue, extended text, RFID, outsert or over-sleeve SMB can develop a validation package to suit your labeling equipment.
From design qualification (DQ) through installation qualification (IQ), operational qualification (OQ) and process qualification (PQ) we are able to develop a package to suit you.
From design qualification (DQ) through installation qualification (IQ), operational qualification (OQ) and process qualification (PQ) we are able to develop a package to suit you.
From design qualification (DQ) through installation qualification (IQ), operational qualification (OQ) and process qualification (PQ) we are able to develop a package to suit you.
From design qualification (DQ) through installation qualification (IQ), operational qualification (OQ) and process qualification (PQ) we are able to develop a package to suit you.
Check Weighers and line inspection equipment all need qualifying. From design qualification (DQ) through installation qualification (IQ), operational qualification (OQ) and process qualification (PQ) we are able to develop a package of protocols to suit you.
SMB use an efficient, systematic, risk based, approach to developing validation packages to suit your capping equipment. We will produce Validation Master Plans, IQ, OQ, PQ, Summary Reports, CSV, cGMP, GAMP5, SOP’s, URS, FRS, URS and DDS Generation for you as required.
SMB use an efficient, systematic, risk based, approach to developing validation packages to suit your equipment. We will produce Validation Master Plans, IQ, OQ, PQ, Summary Reports, CSV, cGMP, GAMP5, SOP’s, URS, FRS, URS and DDS Generation for you as required.
From design qualification (DQ) through installation qualification (IQ), operational qualification (OQ) and process qualification (PQ) we are able to develop a package to suit you.
SMB use an efficient, systematic, risk based, approach to developing validation packages to suit your data acquisition systeme. We will produce Validation Master Plans, IQ, OQ, PQ, Summary Reports, CSV, cGMP, GAMP5, SOP’s, URS, FRS, URS and DDS Generation for you as required.
From design qualification (DQ) through installation qualification (IQ), operational qualification (OQ) and process qualification (PQ) we are able to develop a package to suit you.
SMB use an efficient, systematic, risk based, approach to developing validation packages to suit your Advisory Control System. We will produce Validation Master Plans, IQ, OQ, PQ, Summary Reports, CSV, cGMP, GAMP5, SOP’s, URS, FRS, URS and DDS Generation for you as required.
As an experienced and full-service group, SMB has validated Heating, Ventilation, and Air Conditioning (HVAC) systems and their microprocessor controllers in multi-unit, multi-zone manufacturing/R&D facilities.
Validation of an HVAC system requires a thorough understanding of the facility design, and the purpose of each zone/room in the facility. What are the areas and zones in the facility? What are their classes? What area(s) does each particular Air Handling Unit (AHU) service? Are these 100% fresh air supply AHU's, or do they incorporate return air? What control system is in place to monitor and regulate air temperature, humidity, and pressure differentials? How many air changes per hour are required for each zone? Each room? These are all questions that need to be answered to understand the design intent of a facility's HVAC system.
Next the validation strategy should be determined, including the length and intensity of the validation effort (number of sampling weeks and number samples in a day), the status of the facility during sampling (Static? Dynamic? Both?), and the sampling strategy (how and where will samples be taken (temperature, humidity, pressure, particulate) and what are the acceptance criteria).
The HVAC system's controller requires careful study, too. Is this a rudimentary system controlling a single AHU, or a complex, microprocessor-based control servicing multiple AHU's? Is the control system part of a Building Automation (or Management) System responsible for security, fire, etc.? How will your validation activities impact the BAS/BMS? Is this functionality being added on to an existing control system? How will your validation activities affect the existing validation? How should the room sampling regime coincide with reporting from the BAS/BMS? What aspects of GAMP should be incorporated into your validation efforts?
Once you have a clear answer to these and other questions, you can begin to write your protocols.
Obviously, the validation of an HVAC system can be a daunting task for a validation department with stretched resources. Make SMB's experience work for you on your next HVAC validation project.
From design qualification (DQ) through installation qualification (IQ), operational qualification (OQ) and process qualification (PQ) we are able to develop a Heating, Ventilation and Air Conditioning validation package to suit you.
Validation of Purified Water Systems requires a thorough understanding of the facility design and the utility itself. For example, in a USP Water System: Does the source water meet EPA drinking water standards? Are procedures in place to test this? If PVC pipe is used, have proper procedures been followed when preparing and installing the pipe? Could any leachables or extractables be introduced into the system from the PVC pipe, the cement or the solvent? What is the design of the processing loops? Does the design avoid standing water in any loop? Have all deadlegs been minimized? What is the appropriate measurement for a "deadleg": 2-, 3-, 4D? What methods are being used to remove contaminants? Particulate? What control system is in place to monitor and regulate water temperature, pH, and conductivity? How is the water being stored? Does it interact with the air in the storage vessel? How is pressure being regulated throughout the purification system and the distribution loop? Does the purified water meet USP standards? These and others are all questions that need to be answered to understand the design intent of a facility's USP Water System.
From design qualification (DQ) through installation qualification (IQ), operational qualification (OQ) and process qualification (PQ) we are able to develop a Purified Water System validation package to suit you.
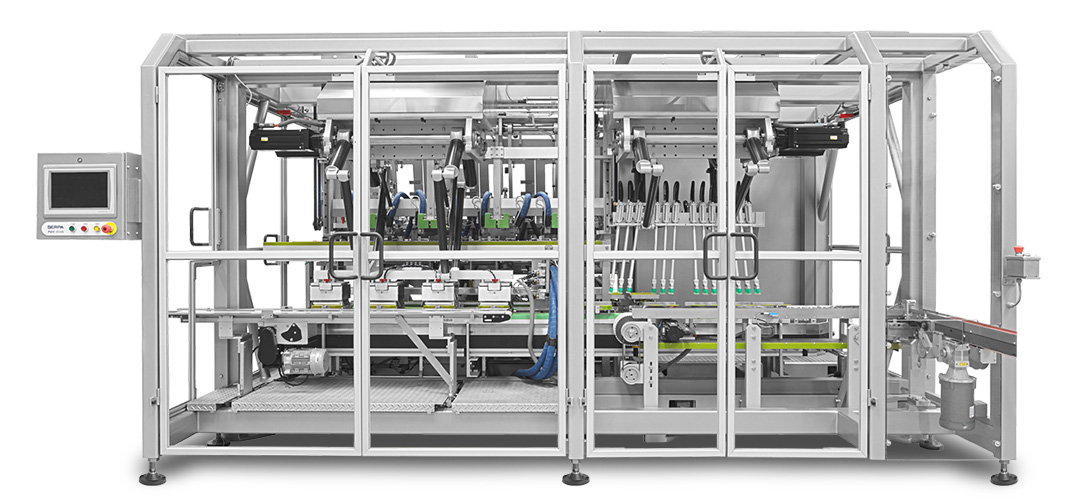